矿热炉又称电弧电炉或电阻电炉。它主要用于还原冶炼矿石,碳质还原剂及溶剂等原料,主要生产硅铁,锰铁,铬铁、钨铁、硅锰合金等铁合金。矿热炉主要分为半密闭和密闭炉两种类型,其中密闭炉产生的尾气含有的可燃成分较多,能够用于燃气内燃机发电。
Submerged arc furnace is also known as electric arc furnace or resistance furnace. It is mainly used for reducing smelting ores, carbon reducing agents, solvents, and other raw materials, and mainly produces ferroalloys such as ferrosilicon, ferromanganese, ferrochromium, ferrotungsten, and silicomanganese alloys. Submerged arc furnaces are mainly divided into two types: semi closed and closed furnaces. The tail gas generated by closed furnaces contains more combustible components, and can be used for gas internal combustion engine power generation.
某矿热炉尾气产生及利用流程
Production and utilization process of tail gas from a submerged arc furnace
在矿热炉生产铁合金的过程中产生的尾气(Furnace off gas,简称FOF)主要成分为CO,以及少量的 H2、 CO2等。其中一氧化碳(CO)气体是由于还原剂中存在碳而形成的,如果还原剂中含有挥发性碳氢化合物,则会形成氢气(H2)。过去,矿热炉尾气通常是直接燃烧后排放,而现在则可以通过高效的燃气内燃机发电,同时利用高温烟气的热能,使能源得到高效充分地利用。
The main components of offgas (FOF) generated during the production of ferroalloys in submerged arc furnaces are CO, as well as a small amount of H2, CO2, etc. Carbon monoxide (CO) gas is formed due to the presence of carbon in the reducing agent. If the reducing agent contains volatile hydrocarbons, hydrogen (H2) will be formed. In the past, the exhaust gas from submerged arc furnaces was usually discharged after direct combustion. However, it can now be generated through efficient gas internal combustion engines, while utilizing the heat energy of high-temperature flue gas to efficiently and fully utilize energy.
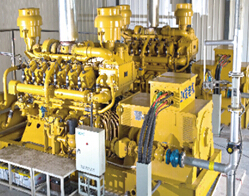
矿热炉尾气的燃烧特性和利用难点
Combustion characteristics and utilization difficulties of tail gas from submerged arc furnace
的热值通常只有天然气热值的1/3左右,也就是说相比于同级输出功率的天然气机型,FOF发电机组的进气量需要增大3倍以上。FOF的抗爆性与天然气也有显著区别,其甲烷指数(Methane Number,简称MN)只有天然气的大约60%左右,这意味着这种气体在内燃机气缸里面更容易发生爆震。所以,燃气发电机组需要通过传感器监测爆震的发生以调整机组的运行状态。另一方面,FOF燃烧时的层流火焰速度(Laminar Flame Speed,简称LFS)却比天然气快许多,这和气体里面氢气的含量比例有关。层流火焰速度是在层流前沿发生氧化反应的速度, 即未燃烧的混合气与火焰前沿之间的相对速度。根据麻省理工学院的研究资料,在当量比(Equivalence Ratio)为2时,5% H2和95% CO组成的混合气的LFS约为50cm/s,而 50% H2和50% CO组成的混合气的LFS可到160cm/s。鉴于FOF特殊的燃烧特性,燃气内燃机的进气系统和控制参数都需要特殊设计以适应其特性,同时还必须满足NOx的排放要求。
The calorific value of FOF power generation units is usually only about 1/3 of the calorific value of natural gas, which means that compared to natural gas models with the same level of output power, the intake volume of FOF power generation units needs to be increased by more than three times. The antiknock performance of FOF is also significantly different from that of natural gas, with its Methane Number (MN) only about 60% of that of natural gas, which means that this gas is more prone to detonation in the cylinders of internal combustion engines. Therefore, gas generator units need to monitor the occurrence of detonation through sensors to adjust the operating state of the unit. On the other hand, the laminar flame speed (LFS) of FOF combustion is much faster than that of natural gas, which is related to the proportion of hydrogen content in the gas. The laminar flame velocity is the rate at which oxidation reactions occur at the laminar front, i.e. the relative velocity between the unburned mixture and the flame front. According to research data from the Massachusetts Institute of Technology, when the equivalence ratio is 2, the LFS of a mixture composed of 5% H2 and 95% CO is about 50 cm/s, while the LFS of a mixture composed of 50% H2 and 50% CO can reach 160 cm/s. Due to the special combustion characteristics of FOF, the intake system and control parameters of gas internal combustion engines need to be specially designed to adapt to their characteristics, while also meeting the NOx emission requirements.
颜巴赫的 DIA.NE XT4系统在气体质量波动时自动调整设置,因此能够适应复杂的运行情况。同时,颜巴赫的LEANOX稀薄燃烧控制技术能够实时控制氮氧化物NOx的排放,确保始终满足严苛的环保要求,使机组排气出口NOx达到250-500mg/Nm3(@5% O2),并且无需SCR等复杂的尾气后处理装置。新的颜巴赫资产管理系统myPlant则能实时监测、控制和预测机组的运行状态,并能提供前瞻性的维护保养建议。
Yanbach's advanced DIA.NE XT4 system automatically adjusts settings when gas quality fluctuates, so it can adapt to complex operating conditions. At the same time, Yanbach's LEANOX lean combustion control technology can control the emission of nitrogen oxide NOx in real time, ensuring that strict environmental requirements are always met, making the unit's exhaust outlet NOx reach 250-500mg/Nm3 (@ 5% O2), and eliminating the need for complex tail gas aftertreatment devices such as SCR. The new Yanbach asset management system, myPlant, can monitor, control, and predict the operating status of units in real time, and can provide forward-looking maintenance recommendations.
本文由合
金尾气发电机组整理发布,您是不是对这些内容有所了解了呢?更多的内容请点击:
我们会有更多精彩内容等你查看。
This article is organized and released by the alloy tail gas generator unit. Have you understood these contents? For more information, please click:
We will have more exciting content waiting for you to check.